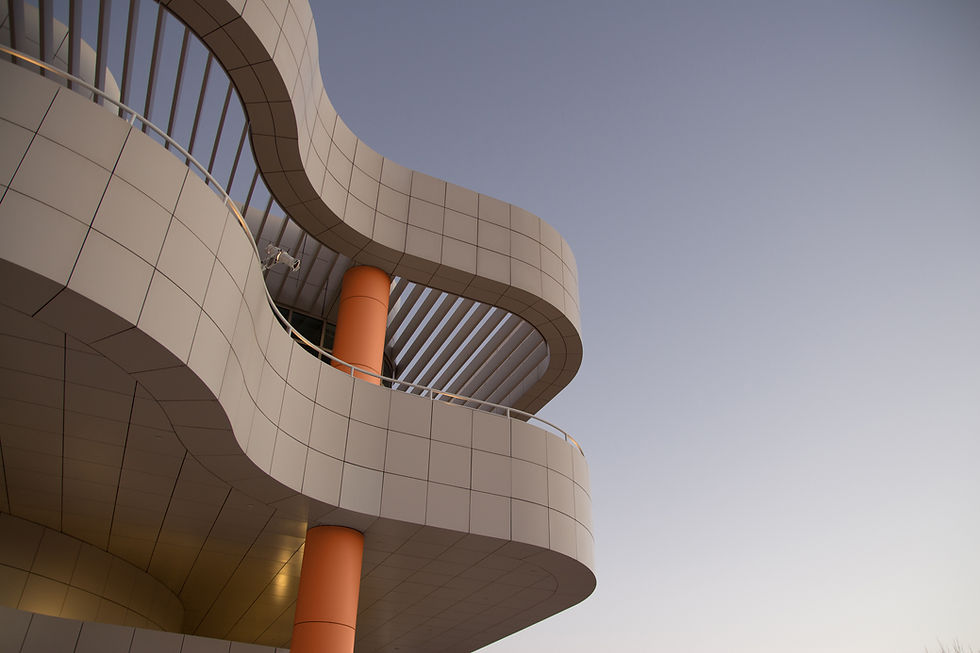
A Beginner’s Guide to Understanding Plastic Injection Molding Processes
Plastic injection molding is a versatile and efficient manufacturing process that is widely used in various industries to produce high-quality plastic parts. Whether you're a business owner, engineer, or simply curious about manufacturing technologies, understanding the basics of plastic injection molding can provide valuable insights into how products are made. This guide will walk you through the fundamental aspects of the injection molding process, from its principles to its benefits.
What is Plastic Injection Molding?
Plastic injection molding is a manufacturing process where molten plastic is injected into a mold to create precise and intricate plastic parts. The process involves heating plastic pellets until they melt, injecting the molten plastic into a mold cavity, and then cooling it to solidify the part. This method allows for the production of complex shapes and high volumes of parts with consistent quality.

How Does the Injection Molding Process Work?
Material Preparation: The process begins with plastic pellets, which are typically made of thermoplastics like polypropylene, ABS, or polycarbonate. These pellets are fed into a hopper and then heated in a barrel until they melt into a liquid state.
Injection: Once the plastic reaches the desired temperature, it is injected into a mold cavity under high pressure. The mold, which is a metal tool designed to shape the plastic, can have various configurations depending on the desired part.
Cooling: After injection, the molten plastic is allowed to cool and solidify within the mold. Cooling time depends on the material and the complexity of the part. Proper cooling ensures that the part maintains its shape and dimensional accuracy.
Ejection: Once the plastic has cooled and solidified, the mold is opened, and the finished part is ejected. Ejection systems, such as pins or air blasts, are used to remove the part from the mold without damaging it.
Post-Processing: In some cases, additional post-processing steps, such as trimming, painting, or assembly, may be required to achieve the final product specifications.
Key Benefits of Plastic Injection Molding
Precision and Accuracy: Plastic injection molding allows for the production of parts with high precision and tight tolerances. The process can achieve intricate details and complex geometries, making it ideal for applications where exact specifications are crucial.
Efficiency and Scalability: Once the mold is created, the injection molding process can produce large quantities of parts quickly and efficiently. This scalability makes it a cost-effective solution for both small and large production runs.
Material Versatility: The process can accommodate a wide range of plastic materials, each with different properties, such as strength, flexibility, and resistance to heat or chemicals. This versatility allows manufacturers to choose the best material for their specific application.
Low Waste Generation: Plastic injection molding is designed to minimize material waste. The process uses only the amount of plastic needed to fill the mold, and excess material can often be recycled or reused.
Design Flexibility: The ability to create complex shapes and features in a single mold enables designers to explore innovative and intricate designs that may not be possible with other manufacturing methods.
Common Applications of Plastic Injection Molding
Consumer Goods: Many everyday products, such as kitchen utensils, electronic housings, and toy parts, are produced using plastic injection molding. The ability to create durable and aesthetically pleasing parts makes it a popular choice for consumer goods.
Automotive Components: Injection molding is used to manufacture various automotive parts, including interior trim, dashboard components, and exterior panels. The process's precision and durability are essential for meeting automotive industry standards.
Medical Devices: In the medical field, plastic injection molding produces critical components for devices such as syringes, surgical instruments, and diagnostic equipment. The process ensures high-quality parts that meet stringent regulatory requirements.
Packaging: Plastic injection molding is widely used for producing packaging solutions, including bottles, containers, and caps. The ability to create custom shapes and features enhances the functionality and appeal of packaging.
Conclusion
Plastic injection molding is a powerful manufacturing process that offers precision, efficiency, and design flexibility. Whether you're looking to produce consumer goods, automotive components, medical devices, or packaging, understanding the basics of injection molding can help you make informed decisions and leverage this technology to its full potential. By grasping the key principles and benefits of plastic injection molding, you can better appreciate how this process contributes to the production of high-quality plastic parts across various industries.