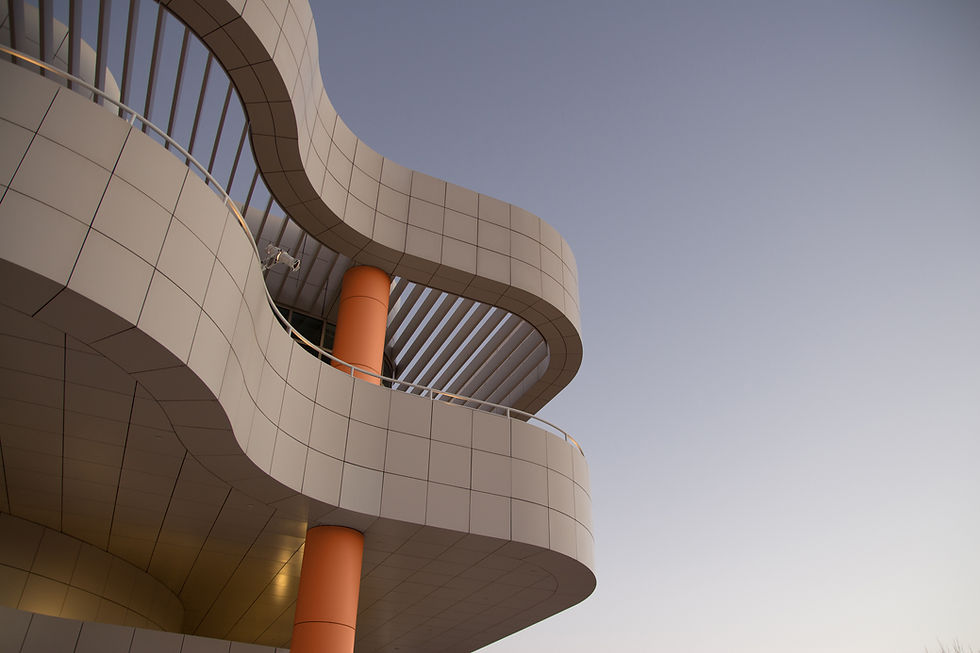
Aluminum Injection Molding for Low-Volume Production: A Comprehensive Guide
In the world of manufacturing, low-volume production has gained popularity as companies seek faster, more cost-effective ways to bring products to market. One method that’s proving to be ideal for this is aluminum injection molding. With its unique advantages, aluminum molds are rapidly becoming a go-to solution for manufacturers needing to produce small to medium batches without sacrificing quality.
This blog will explore every aspect of aluminum injection molding for low-volume production, covering how it works, its benefits, and where it stands in comparison to traditional steel molds.
What is Aluminum Injection Molding?
Aluminum injection molding is a process where molten plastic is injected into an aluminum mold to create a wide range of products. While steel is traditionally used for molding, aluminum is now a popular alternative, particularly for low-volume production. The molds are machined from high-grade aluminum, which offers a range of benefits for manufacturers looking to produce smaller batches of parts.
Why Aluminum Molds for Low-Volume Production?
1. Faster Production Time: Aluminum molds can be machined faster than steel molds, often reducing lead times by 30-40%. This rapid tooling capability makes it an ideal choice for quick-turnaround projects or prototypes.
2. Cost-Effective: Aluminum molds are less expensive to produce compared to steel molds. The material is cheaper, and the machining process is quicker. For low-volume production, where long-term mold durability is not a priority, aluminum offers significant cost savings.
3. Thermal Conductivity: Aluminum has excellent thermal conductivity, allowing for faster cooling of the injected plastic. This results in shorter cycle times, meaning more parts can be produced in less time.
4. Flexibility: Aluminum molds can be designed for various injection molding processes, including over-molding, insert molding, and multi-cavity designs, giving manufacturers flexibility in their production.
5. Ideal for Prototyping: Given their cost-effectiveness and quick production times, aluminum molds are widely used for rapid prototyping: Manufacturers can quickly test part designs and adjust the molds if needed before moving on to higher-volume production.
Aluminum vs. Steel Molds: A Comparison
Let’s compare aluminum and steel molds across several key parameters:
Parameter | Aluminum Molds | Steel Molds |
Cost | Lower cost, ideal for short-run production | Higher cost, suitable for long-run production |
Lead Time | Shorter (2-4 weeks) | Longer (6-12 weeks) |
Durability | Suitable for low to medium volumes | High durability, ideal for large volumes |
Thermal Conductivity | Excellent, faster cooling | Lower, slower cooling |
Typical Application | Prototypes, short-run production | Mass production |
Cycle Time | Shorter due to better cooling | Longer cycle times |
Mold Lifespan | 10,000 - 100,000 parts | 100,000+ parts |
Graph: Cost Comparison of Aluminum vs. Steel Molds for Different Production Volumes
Let’s illustrate the cost comparison of aluminum and steel molds in low, medium, and high-volume production:

Benefits of Aluminum Molds in Low-Volume Production
Cost Savings: For low-volume production, where the mold doesn’t need to endure the stress of producing hundreds of thousands of parts, aluminum molds are a much more affordable option.
Quick Iterations: With faster lead times, aluminum molds are perfect for rapidly iterating designs in the prototyping stage. If a design needs to be modified, aluminum molds can be adapted or re-machined at a lower cost and within a shorter timeframe than steel molds.
Speed to Market: Shorter cycle times and reduced mold production times mean that products can be brought to market faster. This is particularly important in industries where being the first to launch can provide a significant competitive advantage.
Versatility: Aluminum molds can be used across various industries, from automotive to consumer goods and medical devices. Their flexibility makes them suitable for different types of plastic injection molding processes.
Typical Applications of Aluminum Molds
Automotive Industry: Used for producing small runs of automotive components, such as clips, brackets, and custom parts.
Consumer Goods: Ideal for launching new products with shorter life cycles or products that require frequent design changes.
Medical Devices: Useful for prototyping and producing limited quantities of medical devices and components where precision is critical.
Aerospace: Often used in aerospace prototyping and for producing small runs of complex parts with tight tolerances.
Limitations of Aluminum Injection Molding
While aluminum molds offer several advantages, there are a few limitations:
Lower Durability: Aluminum molds wear out faster than steel molds, making them less suitable for long-term, high-volume production. They typically last for up to 100,000 cycles, whereas steel molds can last for over a million.
Lower Resistance to High Pressure: Aluminum molds cannot withstand the same high pressures as steel molds, which can limit their use for certain applications requiring very strong materials or very intricate designs.
When to Choose Aluminum Molds?
Aluminum molds are ideal when:
Rapid Prototyping: When you need quick iterations of a product design.
Low to Medium Production Runs: When producing a few hundred to 100,000 parts.
Cost-Sensitivity: When managing a limited budget for mold tooling.
Short Lead Times: When there’s a need to bring products to market quickly.
Conclusion
For manufacturers seeking low-volume production, aluminum injection molding offers numerous benefits, from cost savings to faster production times. Its flexibility and efficiency make it a strong contender in industries like automotive, consumer goods, medical devices, and aerospace.
Though not suitable for high-volume production due to its lower durability compared to steel, aluminum molds shine in prototyping and small-batch manufacturing, helping companies move from design to market with greater speed and lower costs.