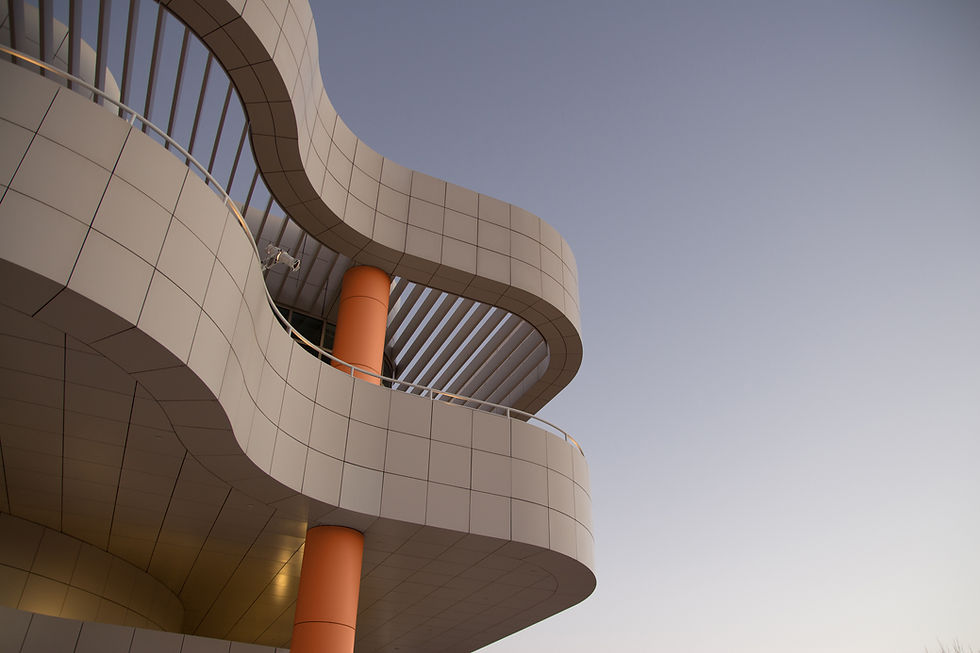
Hard Tooling in Injection Molding: A Complete Guide to High-Volume Production
When it comes to producing large quantities of plastic parts, hard tooling is the gold standard in the injection molding process. While soft tooling is ideal for prototyping and low-volume production, hard tooling excels in mass production, offering durability, precision, and the ability to handle millions of production cycles.
In this blog, we’ll explore what hard tooling is, its benefits, the materials used, and the industries where it plays a vital role.

What is Hard Tooling in Injection Molding?
Hard tooling refers to the use of molds made from hardened metals such as tool steel. These molds are built to withstand the rigors of high-pressure injection molding over long production runs. Unlike soft tooling, which is typically used for short runs and prototyping, hard tooling is engineered for high-volume production, with molds that can last for millions of cycles without significant wear or loss of precision.
Why Use Hard Tooling?
There are several compelling reasons why manufacturers choose hard tooling for their injection molding needs:
Durability: Hard tooling molds are made from high-strength materials like steel, designed to endure repeated injection cycles. This durability makes them ideal for mass production, where the mold needs to produce large quantities of parts over its lifespan.
Precision and Consistency: The hardened steel molds used in hard tooling offer exceptional dimensional accuracy and repeatability. For industries that require parts with tight tolerances—such as automotive or aerospace—hard tooling ensures that every part produced meets exact specifications.
Long-Term Cost Efficiency: While hard tooling has a higher upfront cost compared to soft tooling, it becomes more economical over time due to its longevity and ability to produce large quantities of parts. The cost-per-part decreases significantly in high-volume production, making it a cost-efficient choice for long-term projects.
Compatibility with High-Performance Materials: Some plastic materials, such as high-temperature engineering plastics, require the use of hardened steel molds. Hard tooling can withstand the extreme pressures and temperatures necessary to mold these specialized plastics without degrading.
Materials Used in Hard Tooling
Hard tooling relies on robust materials that can withstand the high pressures and thermal stresses involved in the injection molding process:
Tool Steel (P20, H13, S7, etc.) Tool steel is the most common material used in hard tooling due to its strength, hardness, and wear resistance. Specific grades like P20 and H13 are popular for their ability to handle repeated molding cycles while maintaining precision.
Stainless Steel In applications where corrosion resistance is critical (e.g., medical or food-grade parts), stainless steel is sometimes used for hard tooling. While more expensive, it ensures that molds do not degrade in harsh environments.
Hardened Alloys For even more demanding applications, hardened alloys may be used. These materials offer additional resistance to wear and thermal fatigue, making them suitable for molding abrasive materials or parts that require extreme durability.
Applications of Hard Tooling
Hard tooling is essential in industries that rely on high-volume production and consistency across millions of parts. Here are some of the industries where hard tooling plays a critical role:
Automotive Industry: Hard tooling is widely used in the automotive sector to mass-produce parts such as engine components, interior fixtures, and safety features like airbags and seatbelt systems. With the need for parts that meet strict quality and safety standards, hard tooling ensures consistent output over long production runs.
Consumer Electronics: In the fast-paced world of consumer electronics, hard tooling is crucial for producing everything from smartphone cases to internal components. The durability of the molds allows manufacturers to meet the high demand for consumer products without compromising on precision.
Aerospace and Defense: Aerospace and defense manufacturers rely on hard tooling to produce lightweight yet durable parts for aircraft and military equipment. The ability to consistently meet tight tolerances is especially important in these industries, where safety and performance are paramount.
Medical Devices: The medical device industry requires high levels of precision and reliability, particularly for components like syringes, surgical tools, and diagnostic equipment. Hard tooling ensures that medical devices meet regulatory standards and perform flawlessly in critical applications.
Limitations of Hard Tooling
Although hard tooling offers many advantages, there are a few limitations to keep in mind:
High Upfront Cost: The initial investment in hard tooling is significantly higher than soft tooling. However, this cost is offset by the long-term benefits when producing large quantities of parts.
Longer Lead Time: Because hard tooling molds are more complex and require specialized materials, they take longer to design and manufacture. This means they are not suitable for projects with tight deadlines or rapid design changes.
Less Flexibility: Hard tooling is not ideal for projects where frequent design modifications are expected. Once the mold is made, altering it is costly and time-consuming.
When to Choose Hard Tooling
Hard tooling is the right choice when:
Mass Production is Required: If your project involves producing thousands to millions of parts, hard tooling offers the durability and precision needed for high-volume manufacturing.
Tight Tolerances and High-Performance Materials are Needed: When working with specialized plastics or parts that require extreme precision, hard tooling ensures consistent quality over long production runs.
Cost-Per-Part Needs to be Minimized Over Time: For long-term projects, the initial investment in hard tooling becomes more economical due to the lower cost-per-part over large quantities.
Conclusion
Hard tooling is a cornerstone of the injection molding process for businesses looking to produce large volumes of plastic parts with precision and durability. While the upfront costs and lead times are higher than soft tooling, the long-term benefits of hard tooling make it an essential choice for high-volume production. Industries such as automotive, consumer electronics, aerospace, and medical devices rely on hard tooling to ensure the consistent quality and performance of their products.
At our company, we offer high-quality hard tooling solutions that are designed to meet the specific needs of your industry. Whether you’re looking for mass production or specialized parts that require extreme precision, our expert team can help you achieve your manufacturing goals. Contact us today to learn more about our hard tooling services.