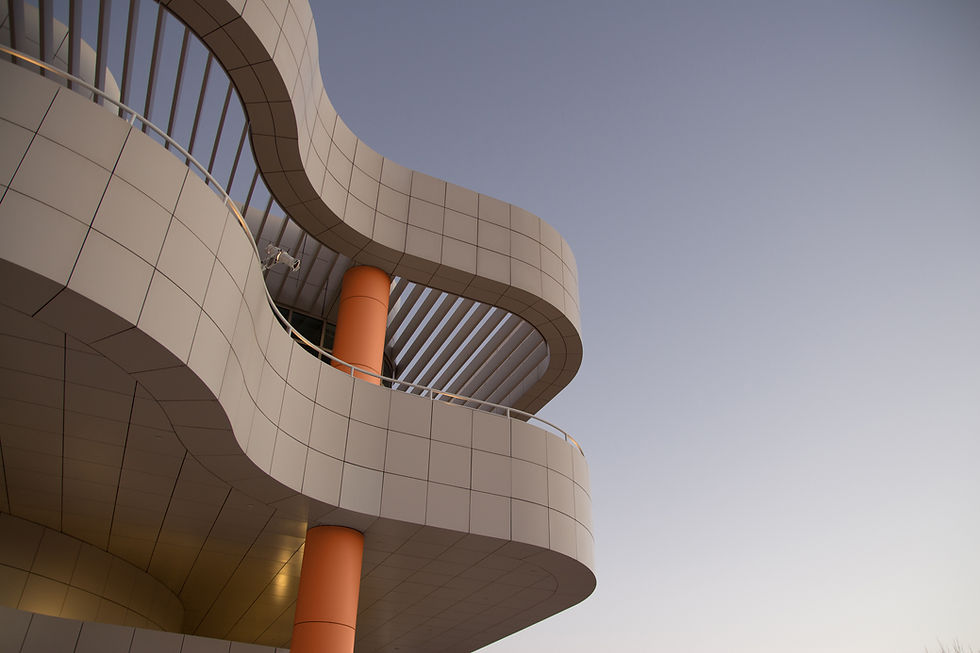
How Economic Changes Affect the Cost of Plastic Raw Materials for Injection Molding: The Role of Oil Prices, Supply Chain Disruptions, and Global Economics
Introduction:
Plastic raw materials, especially granules used in injection molding, are highly sensitive to global economic conditions. Economic factors like fluctuations in oil prices, supply chain disruptions, and broader market changes can significantly influence the cost of these materials. This blog explores how these elements interact and what businesses in the plastic manufacturing industry need to consider to navigate the uncertainties.
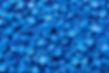
1. The Link Between Oil Prices and Plastic Granule Costs
Plastics are derived from petrochemical processes, making oil a fundamental raw material in their production. As a result, changes in oil prices have a direct and immediate impact on the cost of plastic granules. Here’s how:
Oil Price Increases: When oil prices rise, the cost of producing plastic resins and granules spikes, raising prices for manufacturers. This creates upward pressure on pricing, impacting profit margins unless adjustments are made in pricing strategy or cost efficiency.
Oil Price Decreases: On the flip side, a drop in oil prices can reduce material costs, offering manufacturers some relief. However, these benefits may be delayed as it takes time for lower oil prices to filter through the supply chain to material suppliers.
The cyclical nature of oil prices, driven by geopolitical factors, production policies (e.g., OPEC decisions), and global demand, means that manufacturers need to remain agile in their cost forecasting.
2. Supply Chain Disruptions and Their Ripple Effect
The global supply chain plays a crucial role in determining the availability and cost of plastic raw materials. Here are some key factors that influence the supply chain:
Shipping Delays and Transportation Costs: A disruption in shipping, whether caused by port congestion or geopolitical tensions, can lead to delays in the delivery of plastic granules. This, in turn, pushes prices up as manufacturers face supply shortages and increased transportation costs.
Logistics Bottlenecks: Events like natural disasters, strikes, or even accidents at key logistical hubs can create bottlenecks in the supply of raw materials. For plastic manufacturers, this can mean a sudden surge in prices as demand exceeds supply.
Inventory Management: To mitigate these risks, some manufacturers stockpile raw materials, which can stabilize costs in the short term. However, this strategy has its own costs in terms of storage and cash flow.
3. The Impact of Global Economic Changes
Broader economic trends, such as inflation, currency fluctuations, and trade policies, can also affect the cost of plastic raw materials:
Inflation: Inflationary pressures raise costs across the board—whether it's energy prices, labor costs, or raw materials. Plastic manufacturers must absorb these costs or pass them on to customers, affecting profitability.
Currency Fluctuations: Exchange rates play a role in international trade. For companies importing plastic granules, a weaker local currency can make raw materials more expensive. Conversely, a strong local currency can provide some price relief.
Trade Policies and Tariffs: International trade agreements and tariffs can alter the pricing dynamics for plastic materials. Restrictions or tariffs on imports may increase raw material costs, while favorable trade deals can reduce them.
4. Strategies for Managing Economic Uncertainty
To minimize the impact of economic fluctuations, businesses in the plastic manufacturing industry can adopt several strategies:
Diversifying Suppliers: Sourcing plastic raw materials from multiple suppliers in different regions helps mitigate the risk of disruptions and price surges caused by local economic changes.
Long-term Contracts: Negotiating fixed-price contracts with suppliers can offer stability in material costs, shielding manufacturers from sudden spikes in raw material prices.
Monitoring Economic Indicators: Keeping a close eye on key economic indicators such as oil prices, inflation rates, and shipping costs can help businesses anticipate changes and make informed decisions regarding production and pricing.
Conclusion:
Economic changes—from oil price fluctuations to global supply chain challenges—have a profound impact on the cost of plastic raw materials. Manufacturers need to stay informed and agile, employing strategies that minimize risk and optimize costs. At Venus Plastic, we continuously monitor these trends and adopt proactive measures to ensure that our customers receive high-quality products at competitive prices, despite the complexities of global economics.