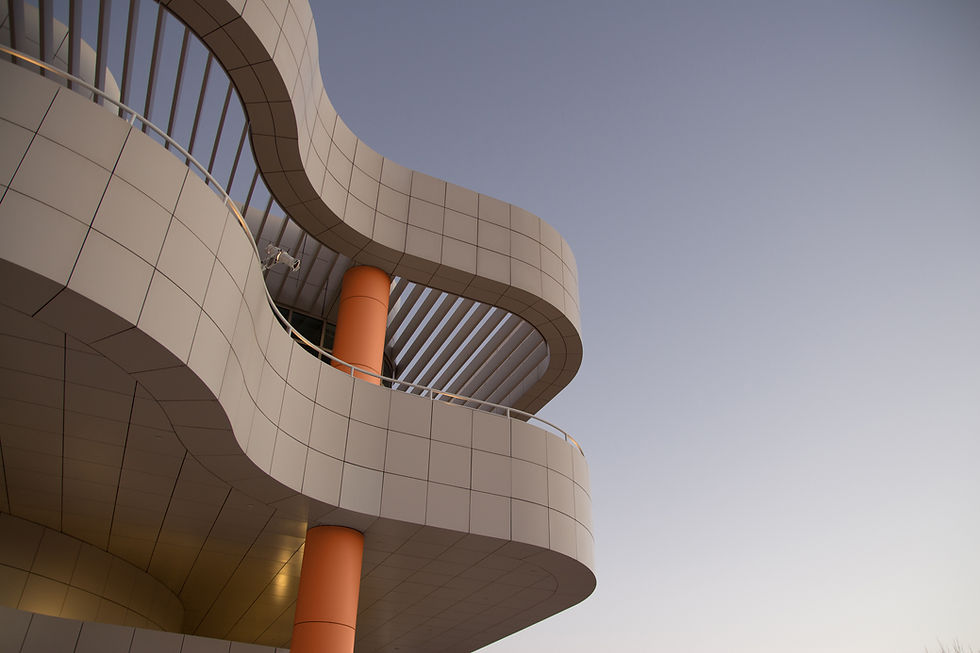
How to Reduce Costs in Plastic Injection Molding Without Compromising Quality
Reducing costs in plastic injection molding without compromising quality is a common goal for manufacturers, especially in today’s competitive market. While it's important to keep production costs low, maintaining the integrity of your product is crucial. Fortunately, there are several strategies to achieve cost efficiency while still ensuring high-quality output. Here’s how to do it.
1. Optimize Part Design
A well-optimized part design can significantly reduce costs. Simplifying the design minimizes the material needed and shortens cycle times, leading to more efficient production. Avoiding unnecessary complexity, sharp corners, and thick walls can not only reduce material use but also make the molding process more efficient.
Using CAD software and mold flow analysis tools can help identify potential design improvements early on, which minimizes production issues and revisions later in the process.

2. Choose the Right Material
Selecting the right plastic material is essential for balancing cost and performance. While high-performance materials may offer superior durability, they can also be expensive. It's important to assess whether these advanced materials are necessary for your product or if a less expensive alternative will meet your needs.
Recycled or blended materials can also be considered, depending on the application. Collaborate with your injection molding partner to identify material options that reduce costs without sacrificing the desired properties of your product.
3. Maximize Cavitation in the Mold
Multi-cavity molds can produce multiple parts in a single cycle, significantly reducing production time and costs for high-volume projects. Although multi-cavity molds may require a higher initial investment, the per-part cost decreases as the production volume increases.
For smaller production runs, using family molds (which produce different parts in the same mold) can also help lower costs by reducing the number of molds required.
4. Minimize Tooling Costs
Tooling is one of the largest upfront costs in plastic injection molding. To reduce tooling expenses, consider using standard mold bases and components rather than fully custom molds. This approach reduces design and machining costs. Additionally, working with your injection molding partner to ensure proper mold maintenance will extend the life of the tooling, further reducing long-term costs.
5. Optimize Cycle Times
Cycle time—the time it takes to produce one part—is a key driver of production costs. Reducing cycle time without sacrificing quality can lead to significant savings. One way to achieve this is by optimizing the cooling time, which accounts for the majority of the cycle. Using conformal cooling channels in the mold can improve heat dissipation and reduce the cooling time.
Additionally, optimizing the injection speed and pressure can help speed up production while maintaining part quality.
6. Reduce Material Waste
Material waste can add up quickly in injection molding. To minimize waste, work on optimizing the gate design and sprue size in the mold, which will reduce excess material. Runnerless molds, such as hot runner systems, eliminate waste material by keeping the plastic in the mold hot until it is used in the next cycle, instead of being ejected and discarded.
Additionally, regrinding and reusing scrap plastic in non-critical parts of the production can reduce the amount of new material needed, further lowering costs.
7. Outsource Production Strategically
Outsourcing to injection molding facilities with a reputation for cost efficiency can also be a smart move. Many overseas manufacturers offer lower labor and production costs, but it’s important to weigh the benefits against the risks, such as shipping delays and quality control issues. By working with a trusted and reliable partner, you can achieve cost savings without compromising quality.
8. Implement Quality Control from the Start
Defective parts lead to rework, material waste, and delayed timelines, all of which increase costs. Implementing robust quality control measures from the start helps catch defects early in the production process, reducing the likelihood of costly rework.
Using techniques like Statistical Process Control (SPC) and automated inspection systems ensures that defects are detected in real-time, preventing further production of faulty parts.
Conclusion
Reducing costs in plastic injection molding doesn't mean cutting corners on quality. By optimizing part design, selecting the right materials, improving mold efficiency, and maintaining strict quality control, manufacturers can achieve significant savings while producing high-quality parts. Collaborating closely with an experienced injection molding partner can help implement these strategies effectively and ensure long-term cost savings.