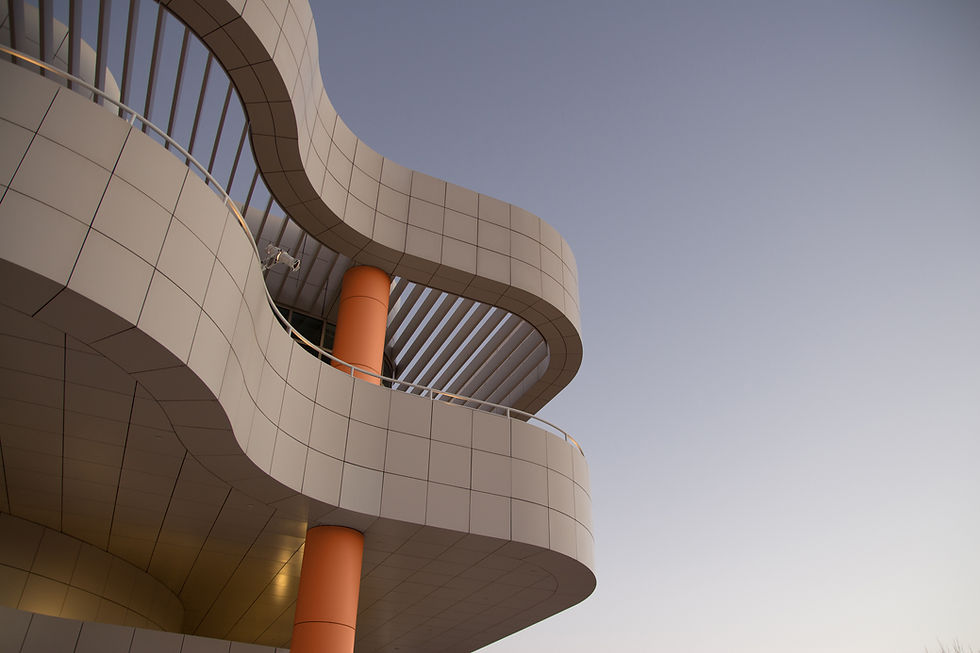
Innovations in Mold Cooling Systems: Improving Efficiency and Reducing Costs
Mold cooling is a critical phase in plastic injection molding, directly impacting production efficiency, part quality, and overall costs. With advancements in technology, cooling systems have become more innovative, offering solutions that enhance the speed and accuracy of the process while reducing operational costs. In this blog, we will explore the latest innovations in mold cooling systems and how they contribute to efficiency and cost savings

1. The Importance of Mold Cooling in Injection Molding
In plastic injection molding, cooling time accounts for a significant portion of the total cycle time. Proper cooling is essential for ensuring that parts solidify uniformly, preventing defects such as warping, shrinkage, or incomplete filling. The faster and more evenly the parts can cool, the quicker the production cycle, leading to increased throughput and reduced costs.
Efficient mold cooling systems are crucial for:
Reducing Cycle Times:Â Shorter cooling times mean faster production.
Improving Product Quality:Â Even cooling ensures that parts maintain dimensional accuracy and mechanical properties.
Minimizing Energy Consumption:Â Advanced cooling methods reduce the amount of energy required for the process, lowering operational costs.
2. Conformal Cooling Channels
One of the most significant innovations in mold cooling systems is the development of conformal cooling channels. Traditional molds use straight-line channels for coolant flow, but these are often inefficient for complex part designs, as they cannot reach certain areas effectively.
Conformal cooling, on the other hand, involves creating cooling channels that follow the contours of the mold cavity. This allows the cooling system to reach every part of the mold more evenly, leading to faster cooling and more consistent part quality.
Key benefits of conformal cooling include:
Faster heat removal, reducing cycle times by up to 30%.
Improved part quality due to uniform cooling.
Less warping and fewer defects, particularly for complex geometries.
3. Advanced Cooling Fluids and Materials
The materials and fluids used in mold cooling systems have also seen significant advancements. New cooling fluids are more efficient at transferring heat and can operate at lower temperatures, leading to reduced cooling times.
Some of the innovations in cooling materials include:
Nanofluids:Â These fluids contain nanoparticles that improve thermal conductivity, enhancing the cooling rate and reducing cycle time.
High-Performance Thermoplastics:Â Advanced materials like polyetheretherketone (PEEK) are now used in mold inserts, allowing for better thermal management and durability in high-temperature environments.
These advanced materials help manufacturers achieve faster cooling rates while maintaining part integrity and reducing long-term wear on molds.
4. Hybrid Cooling Systems
Traditional cooling systems rely solely on water or air cooling, but hybrid cooling systems combine different methods for optimal efficiency. A common approach is combining water cooling with gas-assisted cooling, allowing for rapid initial heat dissipation followed by a more controlled final cooling phase.
Benefits of hybrid cooling systems:
Increased Flexibility:Â Different parts of the mold can be cooled using the method that best suits their specific needs.
Reduced Cycle Time:Â Hybrid systems enable faster initial cooling, reducing the overall cycle time.
Energy Efficiency:Â These systems can be designed to optimize energy usage, lowering operational costs.
5. Active Thermal Management Systems
Another cutting-edge innovation is the development of active thermal management systems. These systems continuously monitor and adjust the cooling process based on real-time data, ensuring optimal cooling performance for each part.
Active thermal management systems use sensors placed throughout the mold to track temperature changes during the injection molding process. The data is fed into a control system, which adjusts the flow of coolant as needed to maintain consistent cooling throughout the mold.
Advantages of active thermal management systems:
Real-time Optimization:Â Cooling is dynamically adjusted for each production cycle, reducing cycle time and improving part quality.
Lower Defect Rates:Â By ensuring consistent cooling, these systems help minimize defects like warping or sink marks.
Enhanced Efficiency:Â Active systems use only the amount of energy necessary for cooling, cutting down on waste and reducing operational costs.
6. 3D Printing in Mold Design
3D printing technology is being increasingly utilized to create more complex and efficient cooling channels within molds. With 3D printing, manufacturers can design cooling channels that would be impossible to produce using traditional machining techniques.
Advantages of 3D-printed cooling systems include:
Custom Geometry: Cooling channels can be designed to perfectly match the part’s geometry, ensuring uniform cooling.
Faster Prototyping and Production:Â 3D-printed molds can be produced faster, allowing for quicker turnaround times on new product designs.
Reduced Cycle Time:Â The ability to place cooling channels closer to the mold cavity enables faster heat dissipation and shorter cycle times.
7. Automation and Integration with IoT
The integration of automation and the Internet of Things (IoT) is transforming mold cooling systems by enabling smart cooling processes. IoT sensors can monitor the mold’s temperature and cooling performance in real-time, automatically adjusting coolant flow and system parameters for optimal performance.
Advantages of IoT-enabled cooling systems:
Data-Driven Insights:Â Continuous data collection allows manufacturers to identify inefficiencies and make adjustments to improve the cooling process.
Predictive Maintenance:Â IoT systems can detect issues before they cause production delays, minimizing downtime and reducing repair costs.
Improved Energy Efficiency:Â Smart systems use data to optimize cooling energy usage, lowering overall operational costs.
8. Conclusion: The Future of Mold Cooling
As plastic injection molding continues to evolve, innovations in mold cooling systems are playing a pivotal role in improving efficiency and reducing costs. Whether through conformal cooling channels, advanced cooling fluids, hybrid systems, or 3D printing, the future of mold cooling is focused on faster production cycles, better part quality, and lower energy consumption.
By adopting these cutting-edge technologies, manufacturers can stay competitive in an increasingly demanding market, delivering high-quality products while keeping costs under control.