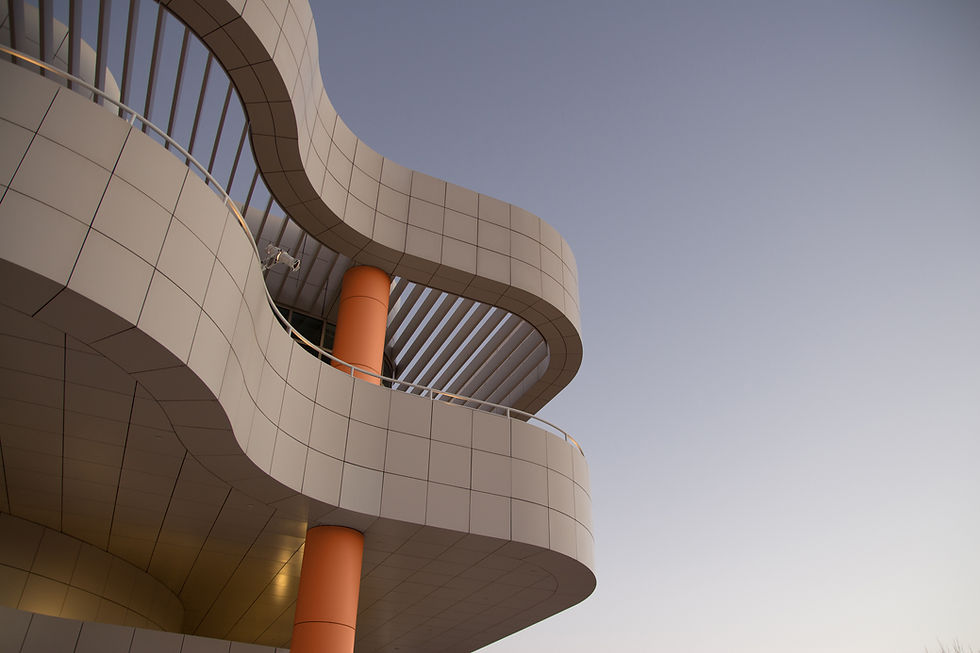
Post-Production Costs in Plastic Injection Molding: What to Expect After Manufacturing
When budgeting for a plastic injection molding project, it's easy to focus on production costs, such as tooling, material, and molding cycles. However, post-production processes play a crucial role in the final cost. These additional steps can significantly impact your project budget, but they are essential for ensuring the quality, functionality, and appearance of the final product. Below, we outline the key post-production costs you should expect after manufacturing:
1. Assembly Costs
Many plastic parts require assembly after the injection molding process, especially if the final product consists of multiple components. Assembly can be automated or manual, depending on the complexity of the product. Common types of assembly include:
Snap-fit assembly
Screw fitting
Ultrasonic welding
Adhesive bonding
The choice of assembly method and the number of parts to be assembled can significantly influence the cost.
2. Finishing and Surface Treatment
Once the parts are molded, finishing may be necessary to enhance the appearance or functionality. Common finishing processes include:
Deburring to remove excess material or sharp edges.
Polishing for a smooth and aesthetically pleasing surface.
Painting or coating to achieve specific textures, colors, or surface protection.
Texturing to add patterns or designs to the part’s surface.
These finishing processes can vary in cost based on the complexity of the design and the materials required.
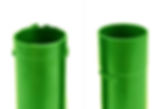
3. Quality Control and Inspection
Ensuring that each product meets the required specifications is critical in the plastic injection molding industry. Quality control includes:
Dimensional inspection to ensure the part is made to precise measurements.
Visual inspections to detect surface imperfections like warping, sink marks, or rough spots.
Functional testing to ensure that the part works as intended in its final application.
Depending on the complexity of the part and the level of scrutiny required, quality control can add a notable amount to post-production costs.
4. Secondary Operations
Some parts may require additional processing after molding to achieve specific features or enhance performance. Common secondary operations include:
Drilling holes or slots.
Tapping threads.
Inserting metal components into plastic parts.
Cutting or trimming to remove excess material or meet precise dimensions.
These operations require specialized machinery or manual labor, impacting the overall cost.
5. Packaging and Labeling
Once the parts are ready, they need to be properly packaged for storage or shipping. Packaging costs depend on:
Type of packaging (e.g., boxes, trays, or bags).
Protective materials used, such as foam, bubble wrap, or cushioning to prevent damage during transit.
Custom labeling or branding if required by the client.
Packaging must not only protect the product but may also serve as an extension of the brand, increasing packaging complexity and costs.
6. Shipping and Logistics
Shipping is a critical cost to consider, especially for international projects. Factors influencing shipping costs include:
Weight and size of the shipment.
Distance and delivery speed.
Customs and import duties for international shipping.
In some cases, clients may require specific logistics services, such as just-in-time (JIT) delivery, which could affect cost and scheduling.
7. Post-Molding Customization
For certain applications, parts may need to be customized after the molding process. This can involve:
Custom branding like engraving or embossing logos.
Color matching and application of custom color schemes.
Part numbering or barcoding for inventory tracking.
These customizations add a unique value to the product but also require additional time and resources.
Conclusion
While production costs form the bulk of an injection molding project’s budget, post-production processes like assembly, finishing, and packaging can significantly add to the total expense. Properly estimating these costs upfront will help you avoid surprises and ensure your project stays within budget. By understanding and accounting for these post-production factors, you can make more informed decisions about your plastic injection molding project and ensure smooth delivery of high-quality, finished products.