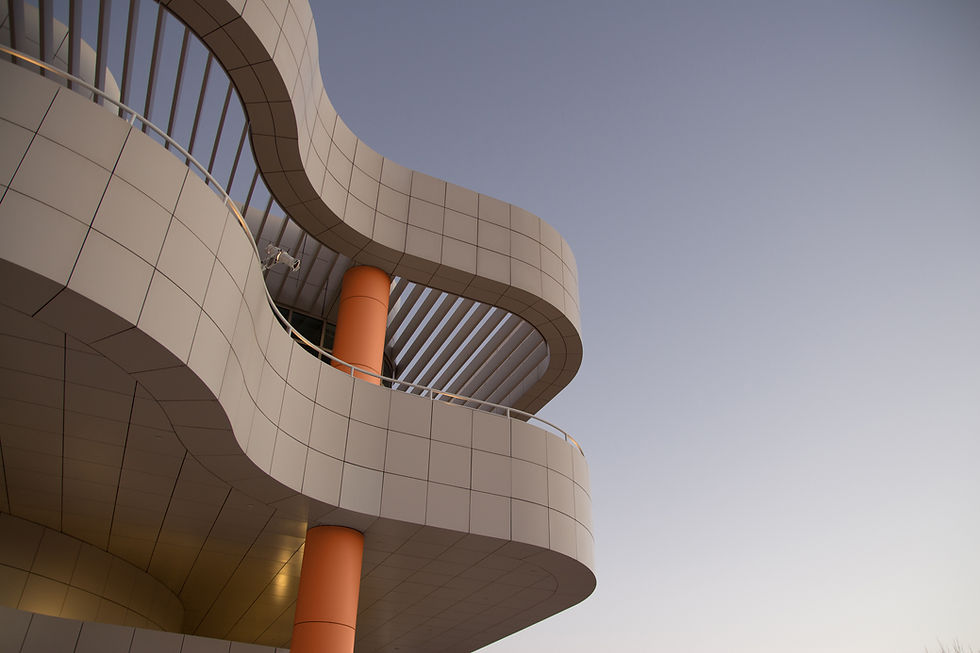
Soft Tooling for Injection Molding: A Comprehensive Guide.
Injection molding is one of the most widely used manufacturing processes for producing high-quality plastic parts. However, before committing to full-scale production, manufacturers often need a cost-effective and flexible solution to validate their designs. This is where soft tooling for injection molding comes into play. Soft tooling offers a fast, economical approach for prototyping, low-volume production, and short-run manufacturing, providing businesses with the flexibility to test and iterate designs without incurring the high costs of hard tooling.

In this guide, we'll explore the basics of soft tooling, its benefits, materials used, key applications, and the industries that can benefit from this versatile manufacturing technique.
What is Soft Tooling in Injection Molding?
Soft tooling refers to the creation of molds using less durable, more cost-effective materials compared to traditional hard tooling. While hard tooling uses robust metals like steel for high-volume production, soft tooling relies on softer materials such as aluminum, silicone, or composite resins.
Soft tooling is ideal for:
Prototyping: Creating prototypes to test designs and functionality before mass production.
Low-Volume Production: Producing small batches of parts economically.
Short-Run Manufacturing: Creating molds for products with limited production runs or frequent design changes.
Benefits of Soft Tooling
Cost-Effectiveness: Developing hard tooling can be expensive, especially for projects with low-volume needs. Soft tooling is significantly more affordable, making it an ideal choice for prototyping and short-run production.
Faster Turnaround: Since soft tooling uses materials that are easier to machine than steel, the lead time for creating molds is much shorter. This allows businesses to accelerate product development and get prototypes or small-batch parts faster.
Design Flexibility: Soft tooling is highly adaptable, making it easier and more affordable to modify designs. This flexibility is invaluable for projects where design revisions or improvements are frequent.
Lower Risk: Soft tooling lets manufacturers test a part’s manufacturability before committing to the more expensive, long-term investment of hard tooling. This reduces the financial risk involved in product development.
Materials Used in Soft Tooling
Soft tooling can be made from a variety of materials, each with its own advantages:
Aluminum
Lightweight: Easy to handle and machine.
Cost-Effective: Less expensive than steel.
Moderate Durability: Aluminum molds can produce up to 10,000 parts, making them suitable for short production runs or pilot projects.
Silicone
Ideal for prototyping, particularly for creating flexible or highly detailed prototypes.
Used in short-lifespan products that require low volumes and frequent modifications.
Composite Materials
Fiberglass and carbon fiber composites offer greater strength and temperature resistance than silicone, at a lower cost than aluminum. These are used when higher strength or temperature resistance is required but still at a lower price point than hard tooling materials.
Key Applications of Soft Tooling
Soft tooling is widely used across various industries that require speed, flexibility, and cost efficiency in product development:
Automotive IndustrySoft tooling allows rapid prototyping of parts such as interior components, lighting, and small mechanical elements, enabling manufacturers to test designs and materials before mass production.
Medical DevicesMedical device manufacturers use soft tooling to create small batches of parts for clinical trials or initial market testing. Frequent design changes in medical products make soft tooling an ideal solution for maintaining flexibility without high costs.
Consumer ProductsIn the fast-moving consumer products sector, soft tooling enables companies to quickly prototype and test new designs, speeding up time to market for products like electronics, home goods, and personal care items.
AerospaceSoft tooling is well-suited for low-volume production of specialized parts in aerospace, where precision and lightweight materials are critical. It allows aerospace companies to prototype and test components before transitioning to higher-volume production.
Soft Tooling vs. Hard Tooling: A Comparison
While soft tooling offers many benefits, it is important to understand its limitations compared to hard tooling:
Feature | Soft Tooling | Hard Tooling |
Material | Aluminum, silicone, composites | Hardened steel |
Cost | Lower initial investment | Higher upfront cost |
Lead Time | Faster turnaround | Longer to develop |
Durability | Suitable for lower volume production | Ideal for high-volume production |
Design Flexibility | Easy to modify | Expensive to alter |
Lifespan | Shorter (thousands of cycles) | Longer (millions of cycles) |
Soft tooling is ideal for projects where prototyping, low-volume production, or short-run manufacturing is needed. However, for large-scale production, hard tooling offers better long-term durability and precision.
Limitations of Soft Tooling
While soft tooling provides numerous advantages, it has some limitations:
Lower Durability: Soft tooling materials degrade faster than steel, making them unsuitable for high-volume production.
Limited Material Compatibility: Some high-performance plastics requiring extreme temperatures or pressures may not be suitable for soft tooling.
Lower Precision: Depending on the materials used, soft tools may not provide the same level of precision or surface finish as hard tools.
When to Use Soft Tooling
Soft tooling is most beneficial when:
Prototyping New Designs: Use soft tooling to test and refine designs before committing to the high cost of steel molds.
Low-Volume Production: For products that will only be manufactured in small quantities, soft tooling provides an economical solution.
Short Production Timelines: Soft tooling can be produced faster than hard tools, making it ideal for projects with tight deadlines.
Conclusion
Soft tooling for injection molding is a practical, cost-effective solution for businesses that need to prototype or produce small batches of parts. With its flexibility, shorter lead times, and lower costs, soft tooling helps streamline product development and enables companies to bring new products to market faster.
Whether you're in the automotive, medical, consumer goods, or aerospace industry, soft tooling can play a crucial role in your product development process. At Venus Plastic, we specialize in high-quality soft tooling solutions tailored to your specific needs. Contact us today to learn how we can support your next project with our expertise in injection molding.