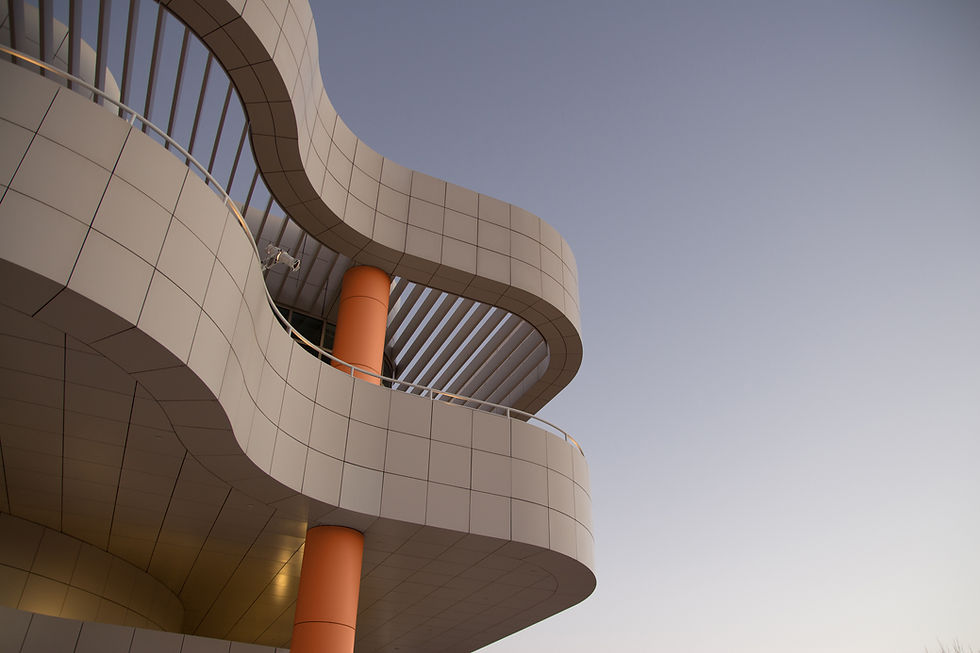
The Effect of Lead Times on Injection Molding Costs
When it comes to injection molding, lead times play a crucial role in determining the overall project costs. Lead time refers to the amount of time between the initial order placement and the final delivery of the injection-molded products. It may seem like a logistical factor, but lead times can significantly impact various cost aspects of your project.
Understanding the effect of lead times on your budget helps in making informed decisions, optimizing processes, and preventing unexpected expenses. Let’s dive into how lead times affect different areas of injection molding costs.

1. Tooling Costs
One of the most significant cost contributors in injection molding is the tooling process. The complexity of the mold, the materials used, and the production capacity all affect how long it takes to create a mold. When lead times are shortened, manufacturers may need to expedite the mold-making process, potentially leading to higher tooling costs. This is because expedited services often come with premium fees for faster delivery and additional labor shifts.
On the other hand, planning for longer lead times can allow manufacturers to spread out the production timeline, helping reduce costs without compromising the quality of the tooling process.
How It Affects Costs:
Shorter lead times: Higher tooling costs due to expedited production.
Longer lead times: Reduced costs through efficient scheduling and standard production processes.
2. Material Sourcing and Costs
The type of material used in the injection molding process is another critical factor influenced by lead times. Short lead times may restrict the availability of certain materials, especially if they are specialty resins or imported products. This can result in increased material costs, as manufacturers might need to source alternatives or pay extra for expedited shipping to meet deadlines.
When you allow for extended lead times, material suppliers have more flexibility in sourcing the correct materials at lower rates, potentially saving your project money.
How It Affects Costs:
Shorter lead times: Higher material costs due to limited sourcing options or expedited shipping.
Longer lead times: Lower material costs as suppliers have more time to procure materials.
3. Production Efficiency
The overall efficiency of the injection molding production process is directly impacted by lead times. When lead times are shortened, manufacturers may need to increase the production speed, which can lead to inefficiencies such as increased cycle times or a higher risk of errors. These inefficiencies not only affect the quality of the final product but also drive up labor and machine operating costs.
With longer lead times, manufacturers can optimize production schedules, ensuring that each part is molded with precision. This leads to fewer errors, less material waste, and lower overall production costs.
How It Affects Costs:
Shorter lead times: Increased production costs due to rushed processes and potential errors.
Longer lead times: More efficient production, leading to lower labor and operating costs.
4. Shipping and Logistics
Shipping costs can also vary depending on lead times. When a project requires fast turnaround, expedited shipping is often necessary to meet deadlines. Expedited shipping costs can significantly inflate the overall budget, especially for large or international shipments. Additionally, rushed logistics can increase the risk of delays or damages, further increasing costs.
Planning for a longer lead time allows for standard, cost-effective shipping options, reducing overall logistics expenses and minimizing the risk of costly shipping issues.
How It Affects Costs:
Shorter lead times: Higher shipping and logistics costs due to expedited services.
Longer lead times: Lower shipping costs with more flexible scheduling and standard shipping methods.
5. Post-Processing and Quality Control
Post-processing tasks like trimming, painting, or assembly, as well as quality control checks, are vital to the injection molding process. When lead times are tight, manufacturers may have to expedite these secondary operations, leading to higher labor costs and a potential compromise in quality. Expedited post-processing can also lead to rushed quality checks, increasing the risk of defects.
A longer lead time allows for thorough quality control and precise post-processing, ensuring that products meet the highest standards without driving up costs due to rushed procedures.
How It Affects Costs:
Shorter lead times: Increased post-processing and quality control costs due to rushed operations.
Longer lead times: Lower costs and improved product quality with a more flexible schedule.
Conclusion
Lead times play a significant role in determining injection molding costs, influencing everything from tooling and material sourcing to production efficiency and shipping. Shorter lead times often lead to higher costs as manufacturers need to expedite multiple aspects of the process. However, with proper planning and a longer lead time, companies can optimize production, lower material and logistics costs, and ensure better overall quality without the need for costly rush services.
Understanding the relationship between lead times and costs helps you make more informed decisions and better manage your injection molding budget.