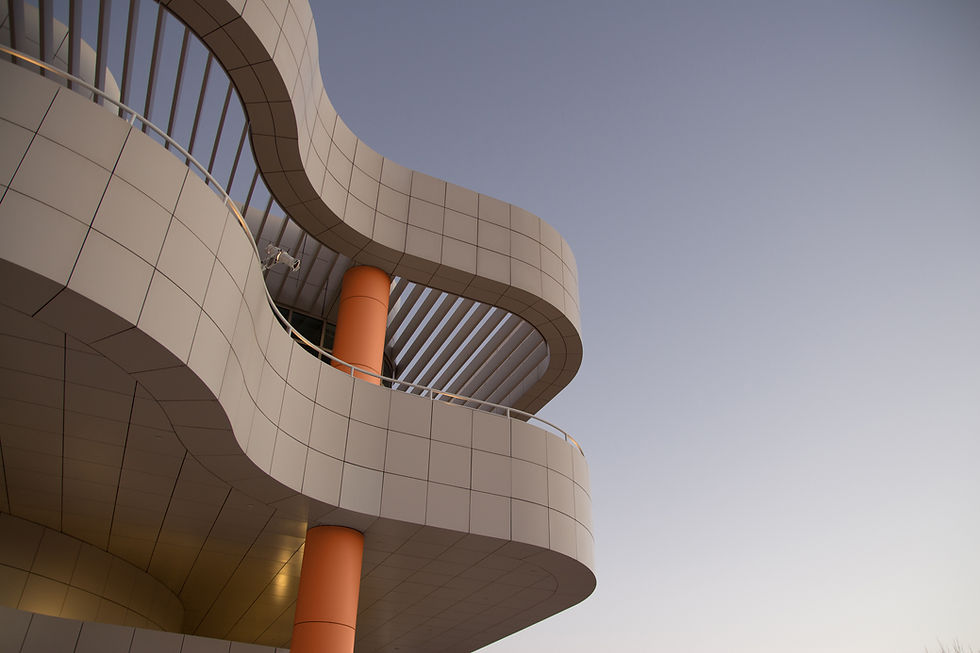
The Importance of Prototyping in Plastic Injection Molding
Prototyping is an essential step in the plastic injection molding process, offering invaluable insights before full-scale production begins. It allows manufacturers to test, refine, and perfect their designs, ensuring that the final product meets all quality and performance standards. Understanding the importance of prototyping in plastic injection molding can help businesses minimize risks, reduce costs, and achieve better results.
1. Why Prototyping Matters in Injection Molding
Prototyping is the process of creating a preliminary model or sample of a product to test its design, functionality, and manufacturability. In plastic injection molding, prototyping helps identify potential issues, allowing for modifications before investing in expensive production molds. This step ensures that the design is optimized for both aesthetics and functionality.
2. Benefits of Prototyping in Plastic Injection Molding
Cost Efficiency:Â By identifying design flaws early in the process, prototyping helps avoid costly mistakes during mass production.
Reduced Time to Market:Â Prototyping accelerates the product development cycle, enabling faster market entry.
Improved Product Quality:Â Prototypes allow for testing and validation of materials, design, and functionality, ensuring the final product meets all specifications.
Flexibility in Design:Â Prototyping enables designers to experiment with different materials, colors, and shapes, offering more flexibility in achieving the desired outcome.

3. Types of Prototyping in Plastic Injection Molding
There are several types of prototypes used in the injection molding process:
3D Printed Prototypes:Â Ideal for rapid design verification, 3D printing offers quick and cost-effective prototyping.
CNC Machined Prototypes:Â Provides high precision and can handle a wider range of materials, ideal for more accurate testing.
Aluminum Mold Prototypes:Â Used when a prototype needs to closely replicate the final product, especially in terms of material properties and production processes.

4. The Prototyping Process in Plastic Injection Molding
The prototyping process typically involves:
Design Review:Â Evaluating the initial design to ensure it meets all functional and aesthetic requirements.
Prototype Creation:Â Using techniques like 3D printing or CNC machining to create a prototype model.
Testing and Evaluation:Â Assessing the prototype for performance, durability, and manufacturability.
Iteration and Refinement:Â Making necessary adjustments based on feedback and retesting until the final design is perfected.
5. Choosing the Right Prototyping Partner
Selecting a manufacturer experienced in prototyping is crucial for a successful product launch. A good partner will not only provide high-quality prototypes but also offer guidance on material selection, design optimization, and cost management. Look for a team that understands your unique needs and can provide tailored prototyping solutions.
6. Conclusion: Prototyping as a Strategic Investment
Prototyping is not just an optional step but a strategic investment in the success of your plastic injection molding project. It allows for early detection of potential issues, ensures that the final product is of the highest quality, and provides a competitive advantage in today’s fast-paced market. Businesses that prioritize prototyping are more likely to achieve efficient production and long-term success.