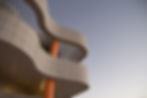
Understanding the Cost Breakdown of Plastic Injection Molding
Plastic injection molding is widely used in the manufacturing industry to produce parts with precision and efficiency. However, understanding the cost breakdown of this process is essential to making informed decisions, especially when balancing quality and budget. In this blog, we’ll explore the main factors that influence the cost of plastic injection molding, including material, tooling, and production volume.
1. Material Costs
The type of plastic material used in injection molding significantly impacts the overall cost. There are several types of plastics, each with different properties, costs, and applications.
Thermoplastics:Â Commonly used due to their versatility and reusability, thermoplastics vary in price depending on their characteristics, such as strength, flexibility, and heat resistance. Examples include polyethylene (PE), polypropylene (PP), and acrylonitrile butadiene styrene (ABS).
Engineering Resins:Â These materials are more expensive but offer superior durability, chemical resistance, and performance. Examples include polycarbonate (PC) and nylon (PA).
Additives and Colorants: Additional costs come from incorporating additives like UV stabilizers, flame retardants, and colorants, which are used to enhance the plastic’s performance and appearance.
The choice of material is directly tied to the product’s intended use, making it crucial to select a material that balances performance with cost-efficiency.
2. Tooling Costs
Tooling, or mold creation, is often the most significant upfront investment in plastic injection molding. The mold is custom-designed for each product, which means that tooling costs can vary based on complexity, size, and precision requirements.
Mold Design Complexity:Â A more intricate design, with fine details, undercuts, or moving parts, will require more time and effort to manufacture, driving up the cost.
Mold Material:Â Molds are typically made from steel or aluminum. Steel molds are more durable and can withstand high production volumes, but they come with a higher price tag. Aluminum molds are cheaper but wear out more quickly, making them suitable for low to medium production runs.
Number of Cavities: A mold with multiple cavities can produce several parts in a single injection cycle, reducing production time and per-part cost. However, this increases the mold’s initial cost.
Tooling Maintenance:Â Over time, molds require maintenance to ensure precision and extend their lifespan, contributing to the overall cost of production.

3. Production Volume
The number of parts being produced plays a critical role in the overall cost structure of plastic injection molding. High-volume production can significantly reduce the per-part cost, while lower volumes tend to be more expensive per unit.
Low-Volume Production:Â For smaller production runs, the cost per part is higher because the fixed costs of tooling and setup are spread across fewer units. This is ideal for prototyping, small batches, or custom projects.
High-Volume Production:Â In large-scale production, the high initial tooling costs are amortized over many parts, resulting in a much lower per-unit cost. This is why plastic injection molding is often favored for mass production, as it becomes highly cost-efficient at scale.
4. Cycle Time and Production Efficiency
The cycle time, or the time it takes to complete one injection molding cycle, directly affects production efficiency and cost. Shorter cycle times mean more parts are produced in a given period, which reduces labor and machine costs. Several factors influence cycle time:
Cooling Time:Â The time required for the part to cool and solidify inside the mold is a significant factor in the cycle. Using efficient cooling systems or materials that cool quickly can reduce this time.
Part Complexity:Â More complex parts may take longer to mold, increasing the cycle time and labor costs.
Automation:Â Incorporating automation, such as robotic arms to remove finished parts, can streamline the process and reduce labor costs, ultimately lowering the overall cost.
5. Secondary Operations and Finishing
In some cases, parts may require additional finishing steps after molding, such as trimming excess material, painting, or assembly. These secondary operations can increase costs depending on the complexity and amount of post-processing required.
Trimming and Deburring:Â Removing excess material from the molded part is a standard post-processing step, especially for more intricate designs.
Surface Finishing:Â Parts may undergo painting, polishing, or texturing to enhance their appearance or functionality, adding to the production cost.
Assembly:Â If multiple components need to be assembled after molding, the assembly process will add additional labor and material costs.
6. Geographic Location and Labor Costs
The location of the manufacturing facility can also influence costs. Labor rates, energy costs, and proximity to raw material suppliers vary across regions, which can affect overall pricing. In regions where labor costs are lower, manufacturers may offer competitive pricing, but it's essential to balance this with considerations for quality and lead time.
7. Conclusion: Balancing Quality and Cost in Injection Molding
Understanding the cost breakdown of plastic injection molding helps businesses make informed decisions about their production strategies. From selecting the right material to optimizing production volume, balancing quality with cost-efficiency is key to a successful project. By considering all the factors—material, tooling, volume, and additional processes—you can ensure that your product meets both performance expectations and budgetary requirements.