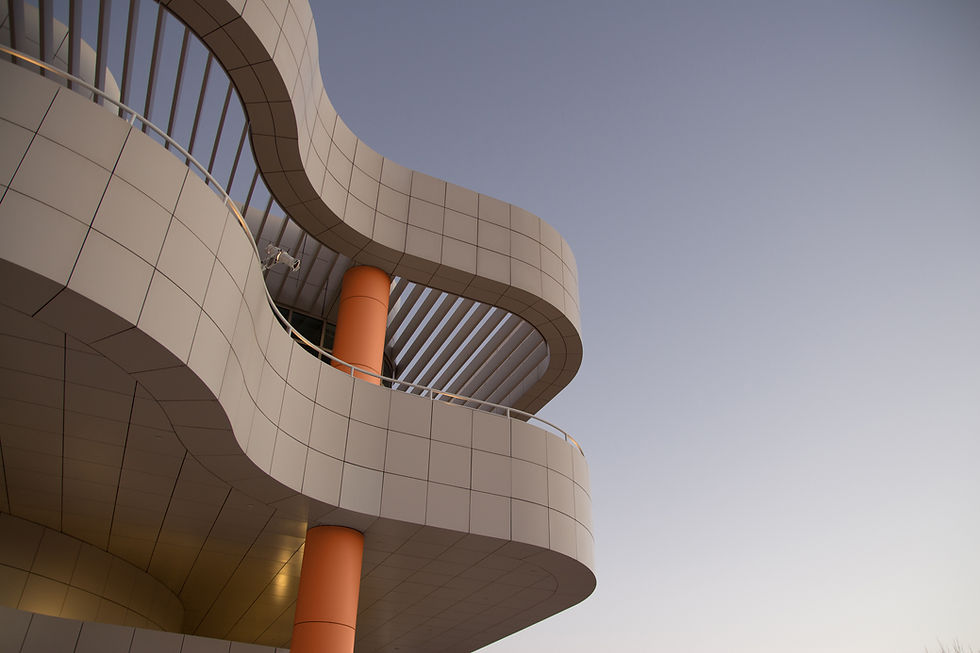
Unlocking Innovation Through Reverse Engineering: Industrial Applications and Benefits
Reverse engineering is a fascinating process where an existing product or system is deconstructed to uncover its design, architecture, or functionality. It plays a crucial role in various industries, helping businesses enhance, replicate, or improve their products by understanding the design of competitors' offerings or outdated systems. In an era of rapid technological advancements, reverse engineering has become a valuable tool for product development and innovation.

What is Reverse Engineering?
Reverse engineering involves taking apart a finished product to understand how it was made, including its structure, components, and workings. It is often employed when original documentation is unavailable or incomplete. Engineers and designers can use this information to recreate the product, modify it, or integrate its features into new innovations.
This process generally includes three steps:
Deconstruction – Disassembling the product or system to identify its components.
Analysis – Studying the components, materials, and software to understand their purpose and how they interact.
Reproduction or Redesign – Using insights from the analysis to recreate or enhance the product.
Key Industries Utilizing Reverse Engineering
Several industries benefit from reverse engineering, as it allows them to optimize products, troubleshoot issues, and innovate. Let’s explore some of these industries:
1. Manufacturing
Reverse engineering is widely used in manufacturing, especially in spare parts production. Often, manufacturers need to replace or improve outdated parts for machinery where no digital models or technical drawings are available. By reverse engineering these parts, companies can create 3D CAD models to reproduce or upgrade components without needing the original blueprint.
2. Automotive
The automotive industry uses reverse engineering to analyze competitor vehicles, improve performance, or recreate components for classic or discontinued models. With the rise of 3D scanning technologies, engineers can quickly scan car parts and reproduce them, reducing development time for new or improved vehicle parts.
3. Aerospace
In aerospace, reverse engineering helps in developing replacement parts for older aircraft models that are no longer in production. This is essential for maintaining operational fleets when original equipment manufacturers (OEMs) no longer supply parts. The ability to recreate exact replicas of critical components helps keep aircraft safe and functional.
4. Medical Devices
Reverse engineering is instrumental in medical device development. Manufacturers reverse engineer existing devices to enhance their designs, optimize functionality, or comply with newer regulations. Additionally, they can use this method to design custom prosthetics and implants that are tailored to individual patients.
5. Consumer Electronics
The consumer electronics industry leverages reverse engineering to stay competitive. By disassembling and studying competitors' products, companies can understand technological advancements, improve their own devices, and reduce time to market for new features.
Benefits of Reverse Engineering
The advantages of reverse engineering extend across industries, making it a valuable tool for innovation and cost savings.
Here are some key benefits:
Product Improvement – Reverse engineering enables companies to enhance existing products by identifying weaknesses and developing better solutions.
Legacy Product Support – Manufacturers can recreate outdated or discontinued components without relying on the original supplier or design files.
Competitor Analysis – By studying competitors' products, businesses can gain insights into advanced technologies and features, helping them stay competitive.
Cost Efficiency – Instead of starting from scratch, reverse engineering helps companies save time and resources by building upon existing designs.
The Role of Technology in Reverse Engineering
Modern reverse engineering relies heavily on technology. 3D scanning and CAD modeling have revolutionized the process, making it faster and more accurate. High-precision scanners can capture even the smallest details of a product, converting physical objects into digital models that can be analyzed, modified, and reproduced with ease. Additionally, software tools like Finite Element Analysis (FEA) and Computational Fluid Dynamics (CFD) allow engineers to test and optimize designs virtually before manufacturing.
Challenges in Reverse Engineering
While reverse engineering offers numerous advantages, it also comes with challenges:
Intellectual Property Concerns – Reverse engineering must be done ethically and legally to avoid infringing on patents or copyrights.
Complexity of Products – Some products, especially those involving complex electronics or proprietary technologies, can be difficult to fully reverse engineer.
Data Accuracy – Inaccurate data from scanning or modeling can lead to incorrect designs, making precision critical.
Conclusion
Reverse engineering is a vital tool in today’s industrial landscape, offering businesses the ability to innovate, improve, and remain competitive. From manufacturing to aerospace, reverse engineering opens doors to understanding existing products and pushing technological boundaries. With the aid of advanced tools like 3D scanning and CAD modeling, the process is now more efficient, driving growth and development across multiple sectors.
Whether your goal is to replace a legacy part, enhance your product's design, or learn from a competitor, reverse engineering provides the insights needed to navigate the complexities of modern industry.